CHRYSLER 2.4L ENGINE FOR SALE
FITS CHRYSLER, DODGE, JEEP, VEHICLES (2010 - 2017)

2.4L CHRYSLER, JEEP REMANUFACTURED ENGINE
ZERO MILES - ALL UPDATES APPLIED
$ 3031.00
- PART NUMBER: FECC24CHRY
- Core Deposit - $370.00 (fully refundable)
- Shipping (round trip) - $300.00
- Warranty - 3 Year / UNLIMITED Miles (upgrades available see below)
- TOTAL: $3031.00 + CORE + SHIPPING
This engine is built back to original OEM specifications.
TINWARE (Oil Pan, Timing Cover, Oil Sump) – $349.00
ADD PREMIUM INSTALLATION KIT – $249.00
INSTALLATION KIT INCLUDES:
- Water Pump
- Thermostat
- Air Filter
- Oil Filter
- Spark Plugs
- Plug Wires or Boots
- Belts
- Hoses
INSTALLATION KITS VARY PER APPLICATION
The BUAP ADVANTAGE™ Engine Re-manufacturing Process
STEP 1) ENGINE BLOCK DISASSEMBLY
Our journey begins with a thorough visual inspection of each engine block for casting defects. We meticulously disassemble the components, inspecting each part for damage and identifying the cause of failure. We remove oil and water passage plugs to guarantee optimal results during thermal cleaning. We select only premium castings for our marine blocks, insisting on replacements in all salt-water applications. For high-performance engines, we utilize premium cores, never employing repaired castings or sleeved blocks, preserving the authenticity of your classic car’s original block casting with our skilled technicians’ craftsmanship.
STEP 2) ENGINE BLOCK THERMAL CLEANING
We elevate engine parts to a new level of clean with our thermal cleaning system. This process evenly distributes heat throughout the chamber, avoiding overheating or warping. Components are heated in an oxygen-deficient atmosphere, decomposing combustible hydrocarbons and leaving parts dry. We use the Ace RKE 230 oven exclusively for cast iron blocks, ensuring ash residue is effortlessly removed in the subsequent stainless steel shot blasting phase.
STEP 3) ENGINE BLOCK SHOT BLASTING
Our shot-blasting method employs stainless steel shot to remove surface contamination like rust, creating a smoother finish. This step is vital for detecting surface and subsurface defects during quality inspection. The peening process imparts compression strength to the metal, preparing it for a preliminary defect inspection.
STEP 4) ENGINE BLOCK MAGNAFLUXING
We use magnetic particle inspection to detect cracks and imperfections in ferrous engine parts, ensuring the highest quality for our cast iron blocks. Before proceeding to aluminum blocks, we explain their specific cleaning, testing, and defect checking processes.
STEP 5) ENGINE BLOCK HIGH PRESSURE WASH
Aluminum engine blocks first encounter our AXE SW20 OS spray cleaning system, which removes all foreign material with its powerful spraying action and multi-integrated nozzles. This step is crucial for a thorough inspection.
STEP 6) ENGINE BLOCK SONIC CLEANING
We use ultrasonic cleaning for aluminum blocks, known as the benchmark in cleanliness. This method reaches inaccessible areas, breaking the bonds that hold small particles to surfaces. Post-cleaning, the block undergoes pressure testing.
STEP 7) ENGINE BLOCK PRESSURE TESTING
We employ the Delta Pressure tester to double-check for pinholes after magnafluxing and dye testing, ensuring the integrity of all castings used in our products.
STEP 8) ENGINE BLOCK PREPARATION
After a complete visual inspection, we repair minor casting defects, remove broken bolts, tap threads, and perform gasket surface repairs to minimize stock removal.
STEP 9) ENGINE BLOCK MACHINING
We use the RMC CNC V40 enclosed machining center for precise and versatile machining. This computerized machine measures and levels blocks, measures deck heights & cylinder bore sizes, eliminating operator error. Our machine determines Ra finish based on block type and gasket used, utilizing CBN cutters and checking surface finish with the Mitutoyo SJ-301.
STEP 10) ENGINE BLOCK ROD RECONDITIONING
The Sunnen LBB-1600 Hone, measuring accuracy within .0001″, is our choice for precision rod reconditioning and pin fitting, ensuring honed bores equal to or better than new rods. High-performance engines are fitted with ARP high-strength bolts and nuts prior to this step.
STEP 11) ENGINE BLOCK HONING
After precise machining, our blocks undergo a second high-pressure wash cycle, ensuring absolute cleanliness for final assembly.
STEP 12) ENGINE BLOCK HIGH PRESSURE WASH
After precise machining, our blocks undergo a second high-pressure wash cycle, ensuring absolute cleanliness for final assembly.
STEP 13) ENGINE BLOCK SONIC CLEANING
We ultrasonically clean all parts prior to assembly, ensuring the ultimate cleanliness level. This method reaches every surface and internal area, providing the cleaning force required for the most stringent standards.
STEP 14) ENGINE BLOCK ASSEMBLY
Each assembler at Buap Engines conducts a thorough visual inspection and measures parts for proper size. We fit blocks with new cam bearings, oil restrictors, relief valves, new water and oil plugs, and more. Cylinder heads are installed with new bolts and gaskets, and each cylinder’s seal integrity is checked. The final inspection by our assembly manager ensures the highest quality for your remanufactured engine.
Buap Engines is committed to delivering engines of exceptional quality and performance. Our rigorous, detailed remanufacturing process ensures every engine we deliver meets our high standards and exceeds your expectations.
THE GOLD STANDARD IN ENGINE REMANUFACTURING
1.) The COMEC ACF200
At Buap Engines, we embrace cutting-edge technology to ensure that every engine we remanufacture meets the highest standards of quality and performance. A cornerstone of our state-of-the-art machinery is the ACF200 Cylinder Boring-Resurfacing Machine. This sophisticated equipment plays a pivotal role in our engine rebuilding process, allowing us to deliver products that consistently exceed expectations.
Precision Engineered for Excellence
The ACF200 is renowned for its precision and versatility. Our skilled technicians utilize this machine’s advanced capabilities to perform intricate machining tasks with unmatched accuracy.
- Dual Functionality: Boring and resurfacing are critical steps in engine remanufacturing. The ACF200 excels in both, ensuring that each cylinder bore is machined to perfection and that every surface finish meets stringent specifications.
- Unrivaled Accuracy: The ACF200’s precision engineering allows us to achieve the tight tolerances required for modern engines. This precision is not just about meeting specifications; it’s about ensuring the longevity and reliability of each Buap Engine.
- Adaptable to All Engine Types: The versatility of the ACF200 means that no engine is beyond our capability. Whether dealing with compact car engines or heavy-duty truck engines, our machine handles them all, making it an invaluable asset in our remanufacturing process.
The Buap Engines Advantage
Incorporating the ACF200 into our remanufacturing process allows us to offer several distinct advantages:
Meticulous Cylinder Machining: Each engine’s cylinders are bored and honed to exact dimensions, ensuring optimal fit and function. This meticulous attention to detail is crucial for the engine’s performance and the vehicle’s overall efficiency.
Flawless Surface Finishing: Proper head gasket sealing is paramount in engine rebuilding. The ACF200 enables us to resurface engine blocks and cylinder heads to precise specifications, ensuring a perfect seal and reliable performance.
Assured Quality and Performance: With the ACF200’s precision, every engine remanufactured at Buap Engines is a testament to our commitment to quality. We don’t just rebuild engines; we enhance them, setting new benchmarks for performance and reliability in the remanufacturing industry.
2.) CNC Crankshaft Grinder
At Buap Engines, we pride ourselves on being at the forefront of remanufacturing innovation, and our CNC Crankshaft Grinder stands as a testament to this commitment. As a leading remanufacturer, we boast the utilization of CNC Crank Grinders, a technology that sets us apart and reinforces our position as an industry pioneer in the United States.
Cutting-Edge Technology in Every Turn
Our CNC Crankshaft Grinder represents the pinnacle of modern engineering, bringing the precision of fully automated production processes, typically exclusive to OEM plants, into our remanufacturing workflow.
One-Chucking Complete Grinding: Designed for efficiency and excellence, the CNC Crankshaft Grinder performs complete grinding of crankshafts in a single chucking. This advanced approach ensures consistency and precision throughout the entire process.
Unmatched Precision and Quality: The machine’s capabilities extend far beyond the current industry standards, offering:
- Stabilized Dimensional Accuracy: Every crankshaft remanufactured at Buap Engines benefits from unparalleled precision, maintaining exacting specifications for every component.
- Superior Surface Quality: The CNC Crankshaft Grinder delivers a finish of the highest quality, ensuring each crankshaft’s longevity and performance.
- Tighter Tolerances: With the advanced technology of our CNC Crankshaft Grinder, we achieve and consistently maintain the tightest tolerances, ensuring each remanufactured crankshaft meets rigorous standards.
3.) Flame Spray Technology
At Buap Engines, we’re committed to innovation and excellence in every facet of our remanufacturing process. Our continuous pursuit of improvement and our investment in the latest technologies underscore this commitment. A shining example of our forward-thinking approach is the integration of state-of-the-art flame spray technology into our operations.
Pioneering with Flame Spray
Recently, Buap Engines has taken a significant leap forward by incorporating the latest flame spray machine into our remanufacturing facilities. Installed and fully operational since 2016, this technology marks a new era in our production capabilities.
Setting New Standards in Finish Quality: The flame spray machine elevates our ability to meet and exceed the finish requirements for engine block cylinder bores. With this technology, Buap Engines effortlessly surpasses the industry benchmarks for remanufacturing current model year engines.
Unparalleled Precision and Durability: Flame spray technology allows us to apply coatings with unmatched precision and uniformity, ensuring each engine block’s durability and performance are maximized. This process not only enhances the quality of the finished product but also extends the lifespan of the engines we remanufacture.
DESCRIPTION
The Tiger is a dynamic 2.4-liter inline-four engine crafted by Chrysler for a range of vehicles, showcasing a commitment to performance and efficiency. Adopting a dual overhead cam (DOHC) configuration, the Chrysler 2.4L Tiger engine is a key member of the Chrysler engine lineup.
Originally introduced in the 2013 Chrysler 200 model, this engine marked a significant step for Chrysler, emphasizing advanced technology and fuel efficiency. The initial design featured a multi-point fuel injection system and an innovative variable valve timing mechanism, ensuring a balance between power output and fuel economy.
As the years progressed, the Tiger engine underwent continuous improvements. In 2016, Chrysler introduced a revamped version with enhancements in combustion efficiency, resulting in improved horsepower and torque figures. The Tiger engine’s evolution showcases Chrysler’s commitment to staying at the forefront of automotive engine technology.
Moving into the 2020 model year, the Tiger engine experienced further advancements, particularly in electronic control systems and precision engineering. These refinements contributed to an overall boost in performance, making the Chrysler 2.4L Tiger engine a reliable powerhouse for a variety of Chrysler vehicles, including the Chrysler 200 and Jeep Cherokee.
Buap Engines takes pride in specializing in remanufactured gasoline engines tailored for diverse automotive applications. Our comprehensive packages include the cylinder block, rotating assembly, cylinder head, valve train, and installation gasket set (oil pump not included).
Distinguishing ourselves from conventional practices, Buap Engines employs a meticulous blueprinting process for all long blocks, ensuring top-notch quality. Our commitment to excellence is evident in the replacement of damaged crankshafts, cylinder blocks, and cylinder heads with brand-new components rather than opting for repairs. Utilizing materials from the same suppliers as the OEM and employing precision machining on CNC equipment, Buap Engines guarantees adherence to or even surpassing OEM specifications in every remanufactured gasoline engine.
Overview
Metric | Value |
---|---|
Engine family | Tiger |
Displacement | 2.4 liters |
Aspiration | Gasoline |
Configuration & cylinders | Inline-four |
Vehicle engine orientation | Transverse |
Valve configuration | Dual overhead cam (DOHC) |
Assembly sites | Detroit, Michigan, USA |
Predecessor | Chrysler 2.0L Tigershark Inline-four |
Successor | Currently none |
TECH UPDATES
- Bore and hone all cylinders to OEM clearances, ensuring precision within .0001 of an inch.
- Decking of cylinder head(s) and block for optimal straightness.
- Cutting valve seats and valves to the proper degree.
- Line boring and honing of crankshaft/camshaft tunnels for enhanced durability.
- Ground and polished crankshaft, coupled with a new or remanufactured camshaft(s) for improved performance.
- Installation of new main bearings, rod bearings, pistons, piston rings, lifters, pushrods (if equipped), timing components, oil pump, and head bolts.
Component Highlights:
- Bore and Hone: Ensures cylinders are machined to OEM specifications, maintaining precise clearances.
- Decking: Enhances straightness for optimal engine performance.
- Valve Seat and Valve Cutting: Precision work to optimize valve functionality.
- Line Boring/Honing: Reinforces crankshaft and camshaft tunnels for increased durability.
- Crankshaft and Camshaft: Ground, polished, and replaced for improved efficiency.
- New Bearings, Pistons, and Timing Components: Vital components replaced for longevity and performance.
- Internal Gaskets and Seals: Comprehensive replacement for a complete engine rebuild.
- Finishing Gaskets: Provided for a seamless finish (may vary per application).
Expertly Remanufactured 2.4L CHRYSLER Engines by Buap Engines & Transmissions
Buap Engines & Transmissions is your trusted partner for 2.4L CHRYSLER engine remanufacturing, offering unmatched quality and performance. Our state-of-the-art remanufacturing process involves precision engineering and the use of high-grade materials, ensuring each engine surpasses original specifications for durability and reliability.
Comprehensive Warranty Support for Your Peace of Mind
We back our remanufactured 2.4L CHRYSLER engines with an industry-leading warranty, reflecting our commitment to quality and customer satisfaction. This robust warranty coverage is our guarantee of reliability, offering you peace of mind with every purchase.
Tailored Consultation to Match Your Vehicle’s Needs
Our team of experts is dedicated to providing personalized consultation services, ensuring that your 2.4L CHRYSLER engine selection is perfectly aligned with your vehicle’s performance requirements. We focus on understanding your needs to recommend the best engine solution, promising optimal performance and seamless integration.
Transform Your Vehicle with a Remanufactured 2.4L CHRYSLER Engine
Opting for a remanufactured 2.4L CHRYSLER engine from Buap Engines & Transmissions means choosing an upgrade that enhances your vehicle’s efficiency, power, and reliability. Explore our selection of premium remanufactured engines today and take the first step towards a superior driving experience.
VEHICLE FITMENTS
IF YOU DON’T SEE YOUR VEHICLE – CALL BUAP SALES
Vehicle | Transmission | Drive Wheels | Power @ RPM | Torque (lb-ft) @ RPM |
---|---|---|---|---|
Chrysler 200 (2013 – 2017) | Nine-speed automatic | FWD / AWD | 184 @ 6,250 | 173 @ 4,600 |
Jeep Cherokee (2014 – 2020) | Nine-speed automatic | FWD / AWD | 180 @ 6,400 | 171 @ 4,600 |
Dodge Dart (2013 – 2016) | Six-speed manual / Auto | FWD | 160 @ 6,400 | 148 @ 4,600 |
Ram ProMaster City (2015 – 2020) | Nine-speed automatic | FWD | 178 @ 6,400 | 174 @ 3,900 |
Jeep Renegade (2015 – 2020) | Nine-speed automatic | FWD / 4WD | 180 @ 6,400 | 175 @ 3,900 |
Chrysler Pacifica (2017 +) | Nine-speed automatic | FWD | 287 @ 6,400 | 262 @ 4,000 |
Jeep Compass (2017 +) | Six-speed manual / Auto | FWD / 4WD | 180 @ 6,400 | 175 @ 3,900 |
Chrysler Voyager (2020 +) | Nine-speed automatic | FWD | 287 @ 6,400 | 262 @ 4,000 |
Jeep Cherokee (2021 +) | Nine-speed automatic | FWD / AWD | 180 @ 6,400 | 171 @ 4,600 |
Chrysler Pacifica Hybrid (2017 +) | Continuously Variable | FWD | 260 @ 5,950 | 236 @ 4,000 |
Chrysler 300 (2011 – 2020) | Eight-speed automatic | RWD / AWD | 292 @ 6,350 | 260 @ 4,000 |
Dodge Journey (2011 – 2020) | Four-speed automatic | FWD / AWD | 173 @ 6,000 | 166 @ 4,000 |
Jeep Cherokee Trailhawk (2017 +) | Nine-speed automatic | 4WD | 271 @ 6,500 | 239 @ 4,400 |
Chrysler 300 (2021 +) | Eight-speed automatic | RWD / AWD | 292 @ 6,350 | 260 @ 4,000 |
SPECIFICATIONS
Metric | Value |
---|---|
Bore | 87.5 mm |
Stroke | 101 mm |
Compression ratio | 10.5:1 |
Max power @ RPM | 184 hp @ 6,250 rpm |
Max torque @ RPM | 171 lb-ft @ 4,600 rpm |
Cylinder head | Aluminum |
Cylinder block | Cast iron |
Camshaft drive | Belt |
BREAK-IN PROCEDURE
Use conventional or break-in oil (non-synthetic) for the first 600 miles of operation. Do not drive for long periods at any single speed, always vary your speed. Do not tow a trailer or put other heavy loads on the vehicle. Check the engine oil and coolant levels daily.
At 600 Miles change the engine oil and filter using conventional (non-synthetic) oil. Check fuel and ignition settings; adjust valves (where applicable).

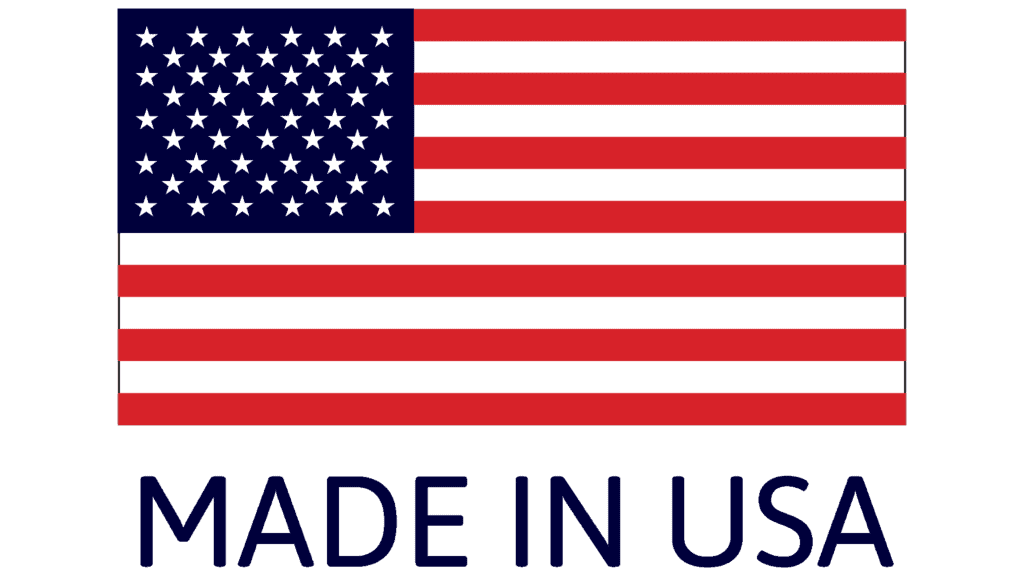